Pomiary i detektory gazu

Podstawowym zadaniem systemów detekcji gazów jest ochrona zdrowia i życia ludzi. Systemy detekcji umożliwiają wczesne wykrycie zagrożeń i zapobieganie powstawaniu atmosfer wybuchowych i stężeń toksycznych, przekraczających stężenia dopuszczalne dla zdrowia.
W przestrzeniach, w których występowanie mieszanin wybuchowych z powietrzem gazów palnych lub par cieczy palnych jest zjawiskiem normalnym lub prawdopodobnym stosowane są urządzenia detekcyjne w odpowiednim wykonaniu przeciwwybuchowym. Są one kalibrowane na poziomie DGW (dolnej granicy wybuchowości) i mierzą stężenia czynników palnych w powietrzu w procentach dolnej granicy wybuchowości (%DGW) lub w tzw. ppm (1% objętościowy = 10000 ppm).
Do ochrony miejsc pracy przy zagrożeniu niebezpiecznymi gazami stosuje się detektory kalibrowane na poziomie wartości odpowiadających NDS lub NDSCh. Są to najczęściej urządzenia:
• stacjonarne wieloczujnikowe z możliwością ciągłej rejestracji wyników pomiarów, przystosowane do generowania sygnałów lokalnej i zdalnej sygnalizacji optycznej i akustycznej oraz sygnałów wyjściowych analogowych lub binarnych; mogą być wykorzystywane do sterowania zewnętrznymi urządzeniami technologicznymi i ochronnymi, np. wentylacją, pompami, zasilaniem w energię elektryczną,
• przenośne, często wyposażone w czujniki do pomiaru stężeń wybranych gazów toksycznych i tlenu, umożliwiające wykonywanie pomiarów w wybranych miejscach w pomieszczeniach lub instalacjach.
Systemy pomiarowe i detekcyjne stacjonarne często mają rozbudowaną strukturę i są stosowane do ciągłych pomiarów stężeń gazów i par wybuchowych oraz toksycznych w dużych obiektach, np. w halach fabrycznych, pompowniach, mieszalniach surowców chemicznych, magazynach butli z gazami. Urządzenia przenośne służą m.in. do pomiarów okresowych stężeń gazów palnych, par cieczy palnych i substancji toksycznych, sprawdzania szczelności rurociągów i ich osprzętu lub sprawdzania stanu zagrożenia przed przystąpieniem do prac, mogących zainicjować wybuch, np. przed spawaniem.
Aparatura gazometryczna wykorzystywana jest w wielu gałęziach przemysłu wydobywczego i przetwórczego – w górnictwie, w przemyśle chemicznym i petrochemicznym, w przemyśle farmaceutycznym w oczyszczalniach ścieków, w kotłowniach i wielu innych. Urządzenia te utrzymywane w sprawności i odpowiednio kalibrowane są często jednym z najważniejszych elementów systemów bezpieczeństwa.
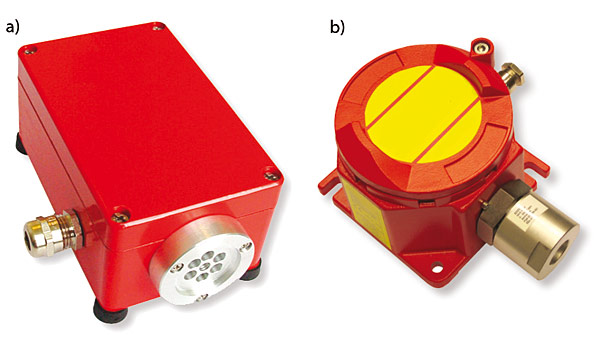
Sensor Sens (a) i ExSens (b) firmy CES
Ogólna charakterystyka czujników
O możliwościach pomiarowych i przydatności do eksploatacji w określonym środowisku w głównej mierze decyduje rodzaj zastosowanego czujnika. W przemysłowej aparaturze gazometrycznej, instalowanej w strefach zagrożonych wybuchem mieszanin gazowych, najczęściej stosowane są czujniki katalityczne, czujniki optyczne z absorpcją w podczerwieni, czujniki elektrochemiczne, półprzewodnikowe i konduktometryczne; dwuprogowe lub wieloprogowe z detektorami w wykonaniu przeciwwybuchowym i systemy pomiarowe z detektorami przeciwwybuchowymi w standardzie 4-20 mA lub z czujnikami mikroprocesorowymi.
W przestrzeniach nie zagrożonych wybuchem, gdzie detekcja zanieczyszczeń gazowych prowadzona jest ze względów sanitarnych w celu nie dopuszczenia do przekroczenia NDS i NDSCh, stosowane są czujniki dwuprogowe i wielodrogowe pomiarowe w standardzie 4-20 mA lub mikroprocesorowe i detektory z własnym zasilaniem i sterowaniem – półprzewodnikowe, elektrochemiczne, optyczne (infra-red).
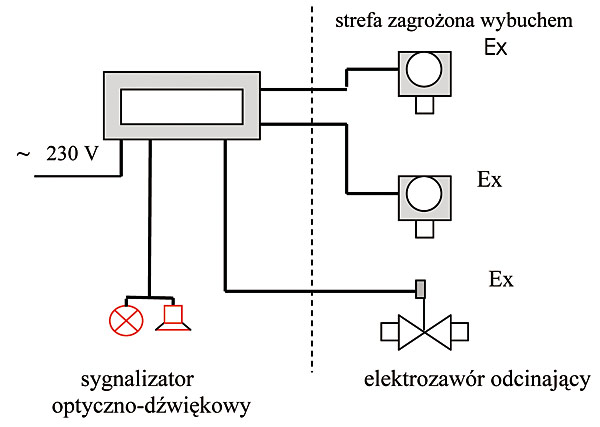
Schemat blokowy prostego systemu gazometrycznego
Czujniki katalityczne
Zasada działania czujnika katality cznego polega na utlenianiu (spalaniu) gazu palnego na powierzchni katalizatora ogrzewanego elektrycznie zazwyczaj do temperatury w granicach od 450oC do 550oC. Najczęściej katalizator ma postać włókna grzejnego z materiału katalitycznego lub impregnowanej katalizatorem porowatej perełki ceramicznej osadzonej na drucie grzejnym. Utlenienie palnego gazu powoduje wyraźny wzrost temperatury elementu grzejnego (pomiarowego) prawie proporcjonalny do stężenia wykrywanego gazu palnego. Obwód pomiarowy zbudowany jest w postaci połowy mostka z dwoma podobnymi do siebie włóknami żarowymi (grzejnymi) lub perełkami umieszczonymi obok siebie. Jedno włókno jest aktywne, zaś drugie pasywne. Włókno pasywne służy jako element odniesienia, pozwalający na kompensację wpływu czynników zewnętrznych – temperatur, ciśnienia i wilgotności, tak aby nie miały one znaczącego wpływu na wynik pomiaru.
Zmiana rezystancji elementu aktywnego pod wpływem ciepła wydzielonego w czasie spalania badanego gazu jest zamieniana na sygnał wyjściowy, zazwyczaj przez niezrównoważenie mostka Wheatstona lub podobnego układu mostkowego. Reakcja spalania badanego gazu powoduje zużycie jego próbki oraz tlenu i konieczne jest ich ciągłe uzupełnianie. Produkty spalania muszą być odprowadzane z miejsca pomiaru.
Czujniki katalityczne mogą działać tylko wtedy, kiedy w otaczającym powietrzu jest wystarczająca ilość tlenu – minimum 10%. Niedostateczna zawartość tlenu w mieszaninie gazowej może spowodować, przy wysokich stężeniach gazu palnego, wskazania przyrządu pomiarowego znacznie poniżej DGW. Dlatego ten typ czujnika może być stosowany tylko do detekcji mieszanin gazowo/powietrznych.
Czujniki katalityczne mogą trwale lub okresowo stracić zdolności pomiarowe w wyniku tzw. zatrucia katalizatora pod wpływem działania niektórych zanieczyszczeń, np. silikonów, czteroetylku ołowiu, związków siarki, organicznych związków fosforu, które albo wytwarzają warstwę stałych produktów spalania na powierzchni katalizatora, albo zmieniają właściwości jego powierzchni. Niekiedy okresowa utrata zdolności katalitycznych może być spowodowana przez niektóre węglowodory halogenowe.
Czujniki katalityczne, zwłaszcza typu perełkowego, przy braku czynników zatruwających w otaczającym powietrzu mogą pracować w sposób ciągły nawet przez kilka lat, ale w wyniku starzenia się i kontaktu ze śladowymi ilościami czynników zatruwających będą progresywnie dryfować i tracić czułość. Z tego względu konieczne są regularne kontrole ich czułości i rekalibracje.
W większości przypadków obudowy czujników katalitycznych wykonane są z przepuszczalnych spieków metali, co umożliwia przedostawanie się gazu do elementu pomiarowego. W przypadku przekroczenia dolnej granicy wybuchowości mierzonego gazu jego mieszanina z powietrzem może być zapalona przez nagrzane części elementu pomiarowego, lecz płomień nie przeniesie się na zewnątrz obudowy i nie zapali otaczającej atmosfery. Próbki mierzonego gazu mogą przedostawać się do czujnika katalitycznego na drodze dyfuzji lub przez zasysanie pompą ręczną lub elektryczną.
Czujniki katalityczne mogą być stosowane do detekcji większości gazów palnych oraz do detekcji mieszanin gazowo / powietrznych w zakresie od 0,1% do 100% dolnej granicy wybuchowości. Przy stężeniach poniżej 0,1 % DGW sygnał jest porównywalny z dryfem zera czujnika. Może to wywoływać nieuzasadnione alarmy. Czas odpowiedzi zależy od rodzaju mierzonego gazu. Gazy o większych rozmiarach cząsteczek i większej ich masie powodują dłuższy czas odpowiedzi i niekiedy mniejszą czułość przyrządu.
Zmiany ciśnienia, temperatury otoczenia w granicach -10oC do 40oC i wilgotności w określonym zakresie nie mają znacznego wpływu na wyniki pomiaru. Jednak im progi alarmowe nastawione są na niższe wartości stężeń, tym zaznaczy się większy wpływ tych czynników. W celu zapobiegania fałszywym alarmom zaleca się nie nastawianie poziomu alarmu poniżej 5% DGW metanu, 10% DGW propanu i butanu oraz 20% DGW w przypadku par benzyny pod warunkiem zastosowania odpowiednich środków zapobiegających toksyczności.
Generalnie zasada pomiaru katalitycznego jest nieselektywna, bowiem wszystkie gazy palne zawarte w powietrzu wywołują sygnał pomiarowy.
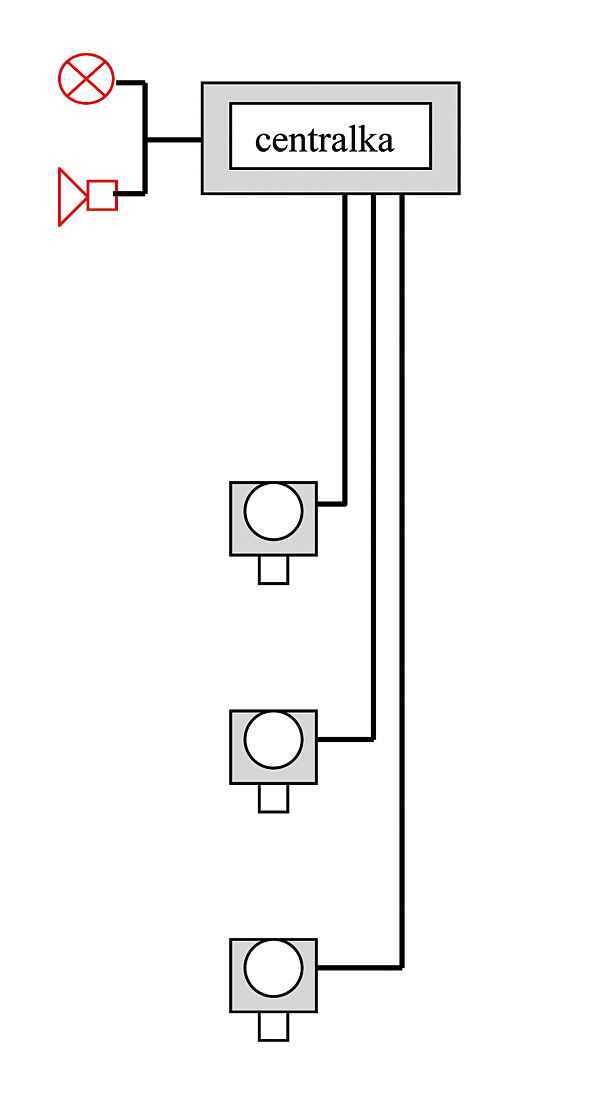
Schemat blokowy systemu gazometrycznego z czujnikami analogowymi (4 – 20 mA); zazwyczaj w systemie znajduje się od 1 do 32 czujników pomiarowych
Czujniki termokonduktometryczne
Zasada działania czujnika termokonduktometrycznego polega na stratach ciepła w wyniku przewodnictwa nagrzewanego elektrycznie elementu rezystancyjnego, np. włókna żarowego, perełki lub rezystora cienkowarstwowego w strudze stale przepływającej próbki gazowej lub w komorze dyfuzyjnej. Czujniki tego typu wymagają zwykle znacznie niższej temperatury niż czujniki katalityczne. W efekcie czas użytkowania w atmosferach, w których nie występują czynniki korodujące, nie jest określony. Próbka mierzonego gazu nie jest zużywana przez czujnik i do pomiaru nie jest potrzebny tlen. Pozwala to na dokonanie odczytu nawet przy zatrzymanym przepływie.
Temperatura nagrzanego elementu pomiarowego wyznaczająca jego rezystancję jest określona przez przepływający gaz i zależy od wielkości jego cząsteczek i innych właściwości fizycznych. Gdy zmienia się skład gazu, zmienia się również temperatura nagrzanego elementu, a zatem i jego rezystancja podobnie, jak w czujnikach katalitycznych. Zazwyczaj, w celu wyeliminowania wpływu zmian temperatury zewnętrznej, w strudze przepływającego gazu lub w zamkniętej komorze pomiarowej umieszczony jest element referencyjny.
Ten typ czujnika jest odpowiedni do pomiarów stężeń gazów, których przewodność cieplna w wymaganym zakresie detekcji zasadniczo różni się od przewodności cieplnej gazu środowiska odniesienia – zazwyczaj powietrza. Publikowane tabele przewodności cieplnej gazów mogą wprowadzać w błąd, gdy w danym środowisku występują inne czynniki wpływające na czułość czujnika, np. konwekcja. Ogranicza to stosowanie tej metody pomiaru do stosunkowo wysokich stężeń, zazwyczaj powyżej dolnej granicy wybuchowości i nie zaleca się jej w przypadku przewidywania stężeń niższych od DGW, z wyjątkiem wodoru i podobnych gazów, na które takie czujniki są specjalnie czułe.
W przypadku mieszaniny gazów odpowiedź czujnika jest nieokreślona, jeżeli nie jest znana proporcja wszystkich gazów składowych mieszaniny łącznie z gazami nie przewidzianymi do pomiaru. W skrajnym przypadku mieszanina gazów o wysokiej i niskiej przewodności cieplnej może znieść odpowiedź badanego gazu.
Czujniki tego typu mogą mierzyć stężenia aż do 100% objętości gazu. Mogą być kalibrowane w dowolnym zakresie aż do 100% wskazanego gazu w określonym gazie tła. Czujniki te są odpowiednie do detekcji gazów o wysokiej lub niskiej przewodności cieplnej w stosunku do powietrza, gdy ono jest środowiskiem odniesienia. Czułość w gazach o wysokiej przewodności cieplnej np. wodoru, helu, neonu w powietrzu jest dobra, zaś w przypadku metanu tylko akceptowalna.
Czujniki termokonduktometryczne nie są selektywne w stosunku do poszczególnych gazów. Odpowiadają one na wszystkie gazy bez względu na to czy są to gazy palne, czy niepalne.
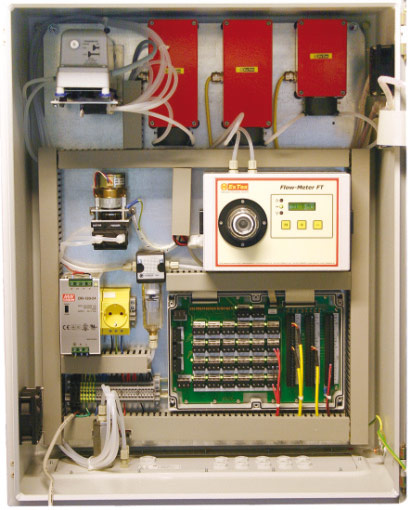
Zintegrowany system pomiarowy IMC 4DA firmy CES
Czujniki absorpcyjne w podczerwieni
Zasada działania spektrofotometrycznych czujników optycznych polega na absorpcji energii promienia wiązki światła w ultrafiolecie, w paśmie widzialnym, lub w części podczerwonej spektrum przez cząsteczki wykrywanego gazu. W praktyce większość czujników tego rodzaju pracuje w widmie podczerwieni (IR). Większość gazów absorbuje energię w paśmie podczerwieni, oprócz gazów jednoatomowych, np. helu, neonu, argonu i gazów o symetrycznych cząsteczkach dwuatomowych, np. wodoru i azotu. Wyjątkiem jest tlen, który wykazuje słabą absorpcję w zakresie długości fal, które zazwyczaj nie są używane do detekcji innych gazów.
Wszystkie gazy mierzalne tą metodą absorbują energię w paśmie podczerwieni charakterystycznym dla ich wiązań chemicznych. Pozwala to na uzyskanie selektywności pomiarów w wyniku doboru odpowiednich pasm detekcji.
Ta metoda pomiaru jest powszechnie stosowana do monitorowania stężeń większości gazów w mieszaninie z powietrzem, bowiem trzy główne składniki suchego powietrza – tlen, azot i argon mają pomijalny wpływ na wyniki pomiaru w powszechnie stosowanym paśmie długości fali. Trzeba jednak zwrócić uwagę na przypadki, w których pasma absorpcji substancji niepalnych i innych nakładają się, co może negatywnie wpływać na wynik pomiaru Najczęściej spotykanymi substancjami zakłócającymi są para wodna i dwutlenek węgla. Dlatego w przyrządach pomiarowych nakładające się długości fal muszą być odpowiednio odfiltrowane.
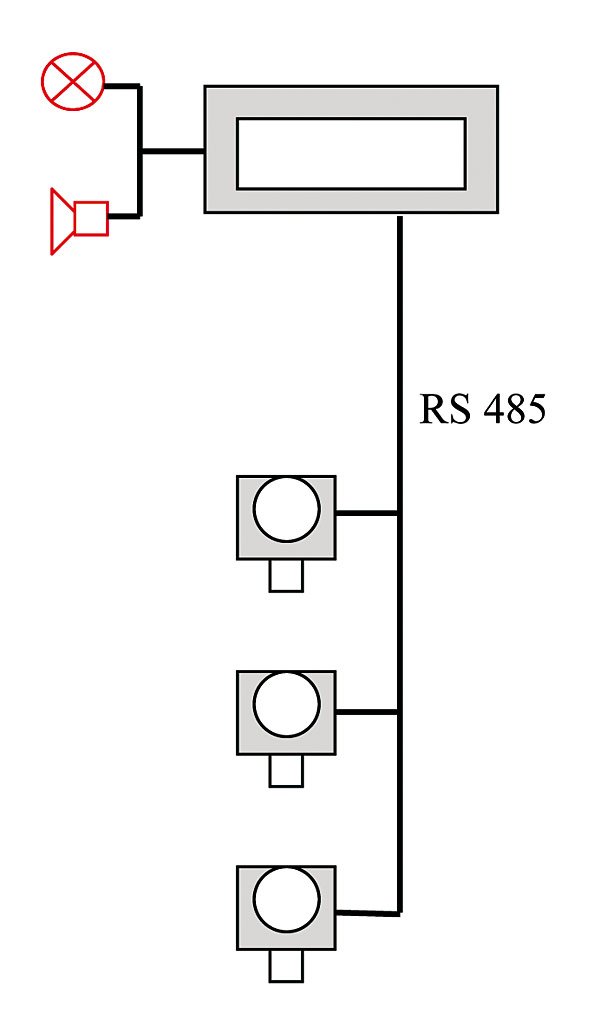
Schemat blokowy systemu gazometrycznego z czujnikami mikroprocesorowymi w standardzie RS 485; zazwyczaj w systemie pracuje od 1 do 64 czujników
Do pracy czujników w podczerwieni nie jest wymagany tlen i nie niszczą one próbki pomiarowej. Przy braku czynników korodujących i oddziaływań mechanicznych spodziewany jest długi okres użytkowania czujnika. Przyrządy na podczerwień charakteryzują następujące cechy:
• wysoka stabilność,
• odporność na zatruwanie,
• możliwość stosowania samodiagnostyki do sprawdzania wyników pomiarów,
• ograniczenie konserwacji dzięki samodiagnostyce.
Czujniki w podczerwieni są kalibrowane do wykrywania poszczególnych gazów lub grupy gazów o podobnych cechach. Inne gazy, których pasmo absorpcji leży poza szerokością pasma kalibracyjnego, nie są wykrywane. Detektory podczerwieni mogą być używane do pomiaru dowolnych zakresów stężeń wielu gazów palnych (z wyjątkiem wodoru) od kilkuset milionowych części do 100 % objętości gazu. Czułość miernika zależy m.in. od długości fali i od długości ścieżki optycznej. Odpowiednie określenie długości fali i długości ścieżki optycznej umożliwia dobór przyrządu do:
• pomiaru całkowitej ilości węglowodorów,
• selektywnego pomiaru pojedynczych składników mieszaniny gazów z powietrzem,
• pomiaru schodzącego do poziomu milionowych części procenta,
• pomiaru aż do 100% objętości gazu palnego,
• pomiaru aż do 100% objętości tlenu.
Czas odpowiedzi przyrządu zależy od czasu potrzebnego do osiągnięcia w ścieżce optycznej stężenia gazu o takiej wartości, jak w mierzonej atmosferze. W przyrządach z zasysaniem może on być krótki. W praktyce czas odpowiedzi jest ograniczony przez osłony chroniące od wpływów zewnętrznych, filtry gazowe i ewentualnie bariery hydrofobowe.
Czujniki półprzewodnikowe
Zasada działania czujnika półprzewodnikowego polega na zmianie rezystywności w wyniku chemisorpcji na ogrzanej powierzchni elementu półprzewodnikowego czujnika wystawionego na działanie gazu innego niż powietrze. O stężeniu gazu wnioskuje się na podstawie zmian rezystancji tego elementu. Zazwyczaj materiałem półprzewodnikowym jest tlenek metalu nagrzewany do temperatury kilkuset stopni Celsjusza.
Czujniki półprzewodnikowe mogą być stosowane do detekcji gazów o różnym stężeniu. Wykazują one odpowiedzi nieliniowe i ich czułość maleje wraz ze wzrostem stężenia badanego gazu. W wielu przypadkach do pracy czujników półprzewodnikowych niezbędny jest tlen. Zmiany jego wilgotności i stężenia wpływają negatywnie na wynik pomiaru. Niektóre półprzewodniki odpowiadają również na substancje inne niż gazy i pary palne.
Związki toksyczne o stężeniach wyższych od tych, w których oddziaływają na czujniki katalityczne, mogą silnie wpływać na czułość czujników półprzewodnikowych – mogą ją ograniczać i niekiedy zwiększać. Przykłady takich substancji to: związki zasadowe i kwasowe, silikony, czteroetylek ołowiu, związki siarki, cyjanki, związki halogenowe. Sposoby ochrony czujników przed oddziaływaniami tego rodzaju substancji podają producenci.
Ogólnie czujniki półprzewodnikowe są nieselektywne i podatne na zakłócenia. Występują znaczne różnice we współczynnikach odpowiedzi w gazach palnych. Wodór jest wykrywany ze znaczną czułością w przeciwieństwie do wielu innych gazów, np. NO2, które mogą wytwarzać sygnały ujemne. Ten typ czujnika jest zazwyczaj stosowany w tanich instalacjach detekcji określonego gazu w założonym zakresie stężeń i w ściśle określonych warunkach.
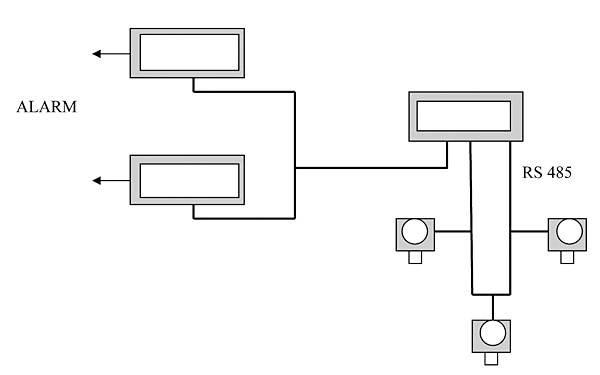
Schemat blokowy systemu z redundancją centralek w układzie 1 z 2; uszkodzenie jednej centralki nie spowoduje niesprawności systemu
Czujniki elektrochemiczne
Zasada działania czujnika elektrochemicznego polega na zmianach parametrów elektrycznych elektrod w zetknięciu z elektrolitem w obecności określonego gazu. Jest to wynikiem reakcji chemicznej redox (redukcji / utleniania) mierzonego gazu na powierzchni elektrody.
Elektrody i elektrolit są zazwyczaj umieszczone w kapsule z półprzepuszczalną membraną pozwalającą cząsteczkom na dyfundowanieprzez interfejs elektroda-elektrolit. W większości konstrukcji na wewnętrznej powierzchni membrany jest umieszczona warstwa szlachetnego lub półszlachetnego metalu tworząca elektrodę, na której będą reagować cząsteczki mierzonego gazu. Elektrody mogą być pokrywane warstwą aktywującą reakcję.
Oprócz elektrody na wewnętrznej powierzchni membrany w kapsule umieszczony jest elektrolit i dodatkowo jedna lub kilka elektrod. Do przystosowania układu do pomiarów różnych gazów wykorzystuje się zmiany zachodzące w materiałach elektrod i w elektrolicie pod wpływem przyłożonego napięcia. Zazwyczaj mierzony gaz jest zużywany podczas reakcji redox. Produkty reakcji przechodzą do elektrody zliczającej.
W czujnikach elektrochemicznych elektrody i elektrolit ulegają stopniowemu zużyciu. Konieczna jest okresowa rekalibracja w celu korekty dryftu zera i czułości. Żywotność takiego aparatu w sprzyjających warunkach wynosi około 2 lat.
Czujniki elektrochemiczne mają ograniczone zastosowania. Są one odpowiednie do pomiaru stężeń wodoru i tlenku węgla do dolnej granicy wybuchowości i tlenu do 25% objętościowych. Spotyka się również czujniki do pomiaru stężeń tlenu do 100% objętościowych. Czujniki te są zazwyczaj stosowane do pomiarów niskich stężeń gazów toksycznych i osobistego monitoringu wielu gazów toksycznych, zwłaszcza H2S; CO, HCN, NH3, PH3, SO2, NO, NO2 i tlenku etylenu.
Czujniki elektrochemiczne są wrażliwe na zmiany warunków zewnętrznych, zwłaszcza temperatury i wilgotności oraz zawartości tlenu i oddziaływania innych gazów.
Detektor jonizacji płomienia (FID)
Zasada działania detektora jonizacji płomienia polega na jonizacji związków organicznych podczas spalania w wewnętrznym płomieniu wodorowym komory spalania. Tak utworzona chmura jonów przemieszcza się w komorze spalania pod występującym między elektrodami gradientem potencjału do kilkuset woltów. Wywołuje to w strumieniu gazu przepływ prądu elektrycznego o bardzo małej wartości, proporcjonalnego do stężenia gazu / pary.
Gazy inertyzujące i szlachetne, tlenki azotu, halogeny, azot, tlen, dwutlenek węgla, czterochlorek węgla i para wodna nie dają żadnej odpowiedzi – są niemierzalne tą metodą. Sygnał dają prawie wszystkie związki organiczne, w większości palne, z wyjątkiem formaldehydu i kwasu mrówkowego.
Ten typ detektora ma doskonałą liniowość w zakresie od dziesiątek milionowych części procenta stężeń do dolnej granicy wybuchowości. Jest on stosowany, gdy głównymi wymaganiami są wysoka czułość, szeroki zakres pomiarowy, odporność na zatrucia i krótki czas odpowiedzi – poniżej 1s. Czujnik ten jest odpowiedni do pomiarów gazów w podwyższonych temperaturach.
Analizator temperatury płomienia (FTA)
Zasada działania analizatora temperatury płomienia polega na pomiarze wzrostu temperatury płomienia gazowego, np. wodorowego o stałym przepływie spowodowanym przez palne zanieczyszczenia w próbce powietrza. Ten rodzaj czujnika jest stosowany do pomiaru całkowitej ilości gazów palnych i par w mieszaninie z powietrzem o stężeniu poniżej DGW, gdy jest wymagany krótki czas odpowiedzi – na ogół poniżej 5 s. Czujnik nie jest selektywny, bowiem odpowiedź zależy tylko od kalorycznych właściwości próbki. Przy wysokich stężeniach odpowiedź nie jest liniowa. Węglowodory halogenowe, np. halony o wysokim stężeniu mogą obniżać sygnał lub nawet zgasić płomień przez redukcję jego temperatury. Czujnik ten jest właściwy do pomiarów gazów w podwyższonych temperaturach.
Detektor fotojonizacyjny (PID)
Zasada pomiaru oparta jest na jon izacji gazów promieniowaniem ultrafioletowym (UV) ze specjalnej lampy o znanej długości fali. Energia fotonów jest zazwyczaj podawana w elektronowoltach eV. Metoda ta nie jest selektywna w zbiorze gazów palnych. Ten typ czujnika stosowany jest, gdy głównymi wymaganiami są: wysoka czułość, odporność na zatrucia i krótki czas odpowiedzi zazwyczaj między 2s a 10s.
Czujnik jest odpowiedni do mierzenia stężeń gazów od poziomów toksycznych do niskich procentów DGW. Jest stosowany do pomiarów stężeń gazów poniżej poziomów niskich, milionowych części procenta w krótkim czasie, np. do detekcji ulotów gazu.
Ogólne zasady instalowania czujników
Detektory gazów mierzą ich stężenia w swoim najbliższym otoczeniu. Dlatego powinny być instalowane w miejscach najwyższych spodziewanych stężeń lub w strumieniu wentylacyjnym doprowadzającym gaz do czujnika z miejsc najbardziej prawdopodobnych wycieków. Czujniki powinny być tak rozmieszczone, aby gromadzenie się gazu wybuchowego było wykryte zanim powstanie mieszanina wybuchowa, a przy detekcji stężeń toksycznych zanim będą osiągnięte najwyższe dopuszczalne stężenia gazu.
Czujniki powinny być tak zainstalowane, aby maksymalnie były ograniczone wpływy środowiskowe, zwłaszcza narażenia mechaniczne, termiczne, wilgoć, promieniowanie IR, nasłonecznienie itp. Przy wyborze miejsc instalowania czujników należy w szczególności brać pod uwagę:
• potencjalne źródła wypływu gazu, np. połączenia kołnierzowe rurociągów, dławice wrzecion zaworów,
• parametry fizykochemiczne gazu/pary – zwłaszcza gęstość względem powietrza,
• charakter możliwego wycieku – naturalno-turbulentny, strumieniowy,
• topografię pomieszczenia i charakterystykę wentylacji,
• obecność źródeł ciepła,
• występowanie substancji zakłócających,
• lokalizację potencjalnych źródeł zapłonu,
• wyposażenie pomieszczeń – rozmieszczenie urządzeń technologicznych, rurociągów, sprzętów, podestów, kratek wentylacyjnych, zagłębień podłogi, które mogą tworzyć strefy martwe pozbawione wentylacji.
Czujniki nie powinny być instalowane:
• w zamkniętych przestrzeniach, np. w szafach, za filarami,
• przy oknach i drzwiach,
• w miejscach, w których temperatura może spaść poniżej 5oC lub przekroczyć 40oC,
• w miejscach, w których kurz może zablokować dostęp gazów/par do czujnika,
• w miejscach o dużej wilgotności,
• bezpośrednio w sąsiedztwie kratek nawiewnych wentylacji.
W przypadku gazów lżejszych od powietrza czujniki powinny być instalowane zawsze powyżej górnej krawędzi okien i drzwi, w pobliżu otworów wywiewnych wentylacji grawitacyjnej i z daleka od otworów nawiewnych wentylacji, nad sufitem podwieszonym, w miejscu nie oddzielonym przegrodą od źródła emisji gazu.
Przy występowaniu gazów cięższych od powietrza i par cieczy – z dala od drzwi i otworów nawiewnych wentylacji, nie nad zagłębieniami w podłodze, w miejscach nie oddzielonych od potencjalnego źródła emisji gazu/pary przegrodami, progami, kanałami w podłodze itp.
W tablicy 1 podane są zalecane wysokości montażu czujników w zależności od gęstości względnej wybranych gazów i par. Czujniki do pomiarów stężeń toksycznych powinny być lokalizowane na wysokości twarzy dorosłego człowieka tzn. około 150 cm do 180 cm nad poziomem podłogi.
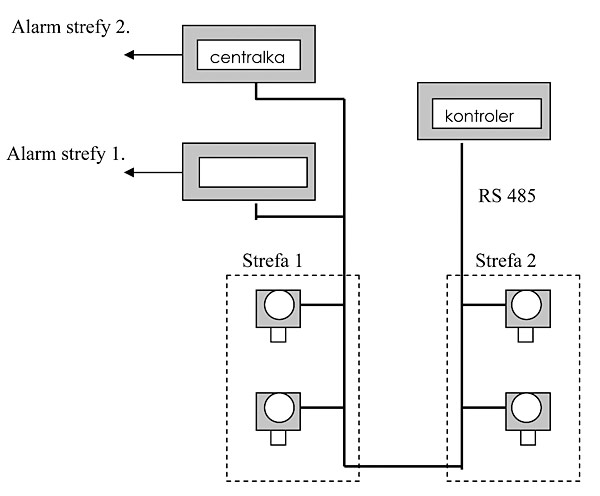
Schemat blokowy systemu składającego się z dwóch niezależnych stref alarmowych
Czujniki mikroprocesorowe
Mikroprocesorowe czujniki stężeń gazów są urządzeniami stacjonarnymi przeznaczonymi do detekcji i monitorowania poziomu stężeń gazów toksycznych i wybuchowych oraz tlenu w otaczającej atmosferze. Czujnik mierzy stężenie określonego składnika w mieszaninie z powietrzem i następnie zamienia je na sygnał analogowy lub cyfrowy. System pomiarowy analizuje wartość zmierzonego stężenia i informuje o przekroczeniu wartości progowych. Czujniki (systemy pomiarowe) mogą znajdować się w następujących stanach pracy:
• normalnym – wszystkie czujniki w systemie pomiarowym wskazują stężenie gazów / par na poziomie niższym od poziomu alarmowego (ostrzeżenia 1),
• ostrzeżenie 1 – co najmniej jeden detektor wykazuje stężenie gazu / pary powyżej progu ostrzeżenia 1, ale żaden powyżej progu ostrzeżenia 2 lub zewnętrzny sygnał na wejściu alarmowym,
• ostrzeżenie 2 – co najmniej jeden detektor wykazuje stężenie gazu / pary powyżej progu ostrzeżenia 2 lub zewnętrzny sygnał na wejściu alarmowym.
Ostrzeżenia i sygnały alarmowe wyrażane są za pomocą sygnałów świetlnych zazwyczaj czerwonych i w formie dźwiękowej o różnych częstotliwościach syreny.
Czujniki przeznaczone do pomiarów stężeń gazów / par w przestrzeniach potencjalnie zagrożonych wybuchem mają obudowy w wykonaniu przeciwwybuchowym, ognioszczelne. Czujnik mikroprocesorowy składa się z następujących podzespołów:
• obudowy ze stopu aluminiowego,
• głowicy pomiarowej zawierającej element wykrywający gaz,
• modułu mikroprocesorowego – wzmacniacza elektronicznego i przetwornika pomiarowego.
Technika mikroprocesorowa pozwala na:
• odczyt i linearyzowanie sygnału wyjściowego,
• kompensację wpływu temperatury otoczenia,
• przełączanie czujnika w określone tryby pracy, np. w tryb kalibracji, alarmu,
• diagnozowanie stanu urządzenia.
Wewnątrz czujnika mikroprocesorowego następuje natychmiastowe przetwarzanie sygnału na postać cyfrową, co podnosi jego niezawodność i odporność na zakłócenia. Wszystkie nastawy i wyniki pomiarów przechowywane są w nieulotnej pamięci. Sygnał wyjściowy z czujnika może być skonfigurowany jako:
• standardowy sygnał prądowy 4 – 20 mA, co pozwala na łatwą integrację czujników z innymi systemami automatyki,
• wyjście szeregowe (cyfrowe) RS 485wg protokółu ModBus,
• wyjście przekaźnikowe.
W zależności od przeznaczenia czujnika mikroprocesorowego do pomiarów określonych gazów producent dobiera rodzaj elementu pomiarowego. Najczęściej są stosowane elementy pomiarowe: półprzewodnikowe, katalityczne, elektrochemiczne, konduktometryczne, infra-red. Czujniki mikroprocesorowe wykrywają m.in. gazy i pary najczęściej spotykane w praktyce przemysłowej przedstawione w tablicy 2.
Urządzenia współpracujące
Przy tworzeniu systemów pomiarowych stężeń gazów / par wybuchowych i toksycznych z czujnikami stężeń współpracują m.in. centralki detekcyjno-alarmowe lub detekcyjno-odcinające, konwertery i kontrolery. Poniżej przestawiono niektóre z nich.
Centralki
Centralki alarmowe (panele sterujące) są jedną z najważniejszych części systemów gazometrycznych do pomiarów stężeń gazów / par wybuchowych i toksycznych oraz tlenu. Są urządzeniami najczęściej op artymi na technice mikroprocesorowej, współpracując z czujnikami i innymi urządzeniami, tworzą systemy detekcji gazów. Centralki są odpowiedzialne za sterowanie pracą systemu i wizualizację jego stanu. Zazwyczaj wyposażone w programowalne wejścia i wyjścia, co pozwala na sterowanie zewnętrznymi urządzeniami ostrzegawczymi i wykonawczymi. Na ogół mają możliwość komunikacji z komputerem PC albo z zewnętrznym sterownikiem PLC. Wyniki pomiaru można odczytać na wyświetlaczu, który jest zazwyczaj w standardzie wyposażenia. Stężenia gazów / par toksycznych i wybuchowych są centralnie obliczane na podstawie danych z czujników pomiarowych. Centralki oferowane są w różnych wersjach montażowych – do montażu na ścianie, na szynie DIN i w szafach 19” Rack.
W zależności od wykonania i przeznaczenia spełniają wszystkie lub tylko niektóre z następujących zadań:
• zasilanie czujników,
• odczyt sygnału cyfrowego – za pomocą interfejsu RS-485 lub analogowego zazwyczaj w standardzie 4-20 mA,
• połączenie z komputerem PC za pomocą interfejsu RS 232 lub RS 485,
• wyświetlanie informacji o stanie atmosfery – sygnalizacja za pomocą diod LED progów ostrzeżeń i alarmów oraz wizualizacja stanów czujnika lub strefy dozorowanej,
• sterowanie urządzeniami współpracującymi za pomocą wyjść przekaźnikowych, np. wentylacją, zaworami odcinającymi,
• generowanie ostrzeżeń i alarmów za pomocą sygnalizatorów optycznych i akustycznych,
• autodiagnostyka i monitoring systemu.
Konwertery
Są to uniwersalne moduły przeznaczone do rozbudowy systemów detekcji gazów / par, służące do łączenia centralek. Ich zadaniem jest konwertowanie sygnału stykowego na sygnał prądowy i umożliwiają:
• zamianę sygnału stykowego na sygnał analogowy 4 – 20 mA,
• diagnostykę obwodu 4-20 mA,
• kontrolę sygnału w jednostce centralnej i jego dalszą obróbkę.
Kontrolery magistrali
Kontrolery magistrali są urządzeniami przeznaczonymi do pracy w systemie pomiarowym. Ich podstawowe zadania to:
• integrowanie systemów składających się z większej niż jedna liczby centralek,
• blokowanie czujników, pozwalające na odłączenie pojedynczego czujnika bez wywoływania awarii i konieczności rekonfiguracji systemu,
• umożliwienie kalibracji czujników i innych czynności serwisowych podczas pracy systemu,
• umożliwianie innym urządzeniom systemowym wykonywania ich dodatkowych funkcji.

Czujnik Alpa S SmArt firmy Atest Gaz do detekcji i pomiaru stężeń gazów w stefie 1 i 2 zagrożenia wybuchem
Magistralny interfejs szeregowy
Urządzenie przeznaczone do pracy w systemach magistralnych RS 485. Jego podstawowe zadania to:
• umożliwienie dostępu do magistrali bez konieczności rozłączania przewodów, np. w czasie konserwacji systemu,
• sygnalizowanie prawidłowego działania obwodu zasilania czujników i linii transmisji sygnałów,
• zabezpieczenie systemu przed przepięciami atmosferycznymi i innymi zakłóceniami zewnętrznymi,
• zabezpieczenie systemu przed skutkami zwarć w obwodzie zasilania lub linii transmisji danych.
Kompaktowe czujniki gazów / par
Zastosowanie techniki mikroprocesorowej pozwoliło na konstruowanie kompaktowych czujników gazów / par. Charakteryzują się one połączeniem w jednym urządzeniu funkcji czujnika (pomiaru stężenia gazu / pary) z wyposażeniem i funkcjami centralki alarmowej – zasilaniem, wyjściami sterującymi, wyświetlaczem i klawiaturą.
Wszystkie urządzenia przeznaczone do tworzenia systemów gazometrycznych w strefach zagrożonych wybuchem mają odpowiednie wykonanie przeciwwybuchowe zgodne z dyrektywą ATEX 100 a i normami serii PN-EN 60079.
Michał Świerżewski
Opracowano na podstawie
materiałów firmowych
oraz stron www